
As a result, we can produce some of the most robust thermoplastic composite pipe in the oil and gas sector, which can cope with extreme operating envelopes, with the least possible material required. We not only share structural analysis results, including stress and strain plots, but we also interface with DNVGL to gain class approval. The ability to simulate m-pipe service life conditions is good for clients. Each test is also strain gauged to allow correlation against the numerical model. The number of physical tests has been dramatically reduced and they now have become confirmatory. Numerous iterations can be assessed to validate the structural integrity of m-pipe. Numerical simulation with ANSYS Workbench FEA (Finite Element Analysis) changed the process allowing our Computer Aided Engineering (CAE) team to rapidly consider different options through efficient scripts within Workbench. We can produce a qualified product, exceeding customer requirements, throughout the design cycle, all the way through to end of life in an incredibly fast timeframe.
#Orcaflex cost software
Simulating service life conditions for TCPĪdvanced simulation software from ANSYS has drastically altered this process through realistic simulations, where actual test behaviour is replicated in the structural response of a numerical model for service life load combinations. Designs for a particular application needed to be physically tested, which very quickly drives up costs and lead times. Prior to investing in advanced simulation software, Magma’s design process was like most in the industry. Meanwhile its flexibility removes the need for complex metrology and bespoke steel manufacture. The lightweight nature of m-pipe means minimises costs as smaller installation vessels are required and installation is simple. Reducing the amount of material reduces the consumption of the fossil fuels.
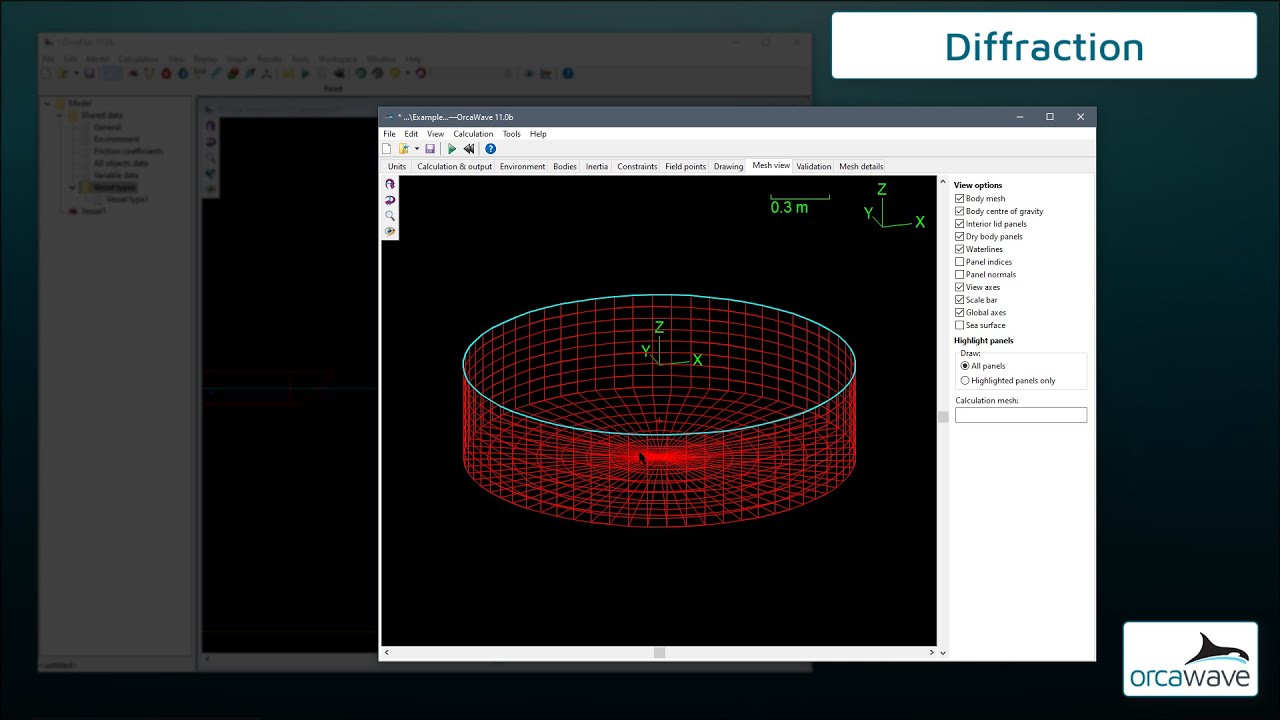
The advanced engineering team at Magma continuously refines the design of m-pipe laminate layers to optimise strength and minimise weight, whilst ensuring the PEEK and carbon fibre thermoplastic composite pipe is cost-effective to manufacture.
